
Think streamlining order fulfillment is only for Amazon-sized operations? Think again. With modest investments and a handful of smart steps, plus a dash of automation, your small business can speed up shipping, shrink mistakes, and boost customer loyalty.
In this guide, we’ll show you exactly how to organize your pick and pack process, layer in affordable tech, and achieve efficiency on a small-business budget. Let’s dive in.
What is Pick and Pack Fulfillment?
The pick and pack fulfillment is part of order processing. It is a barcode-enabled, two-step shipment verification of orders before dispatch. It makes sure each order is double-checked first during the pick phase and again at packing. This helps drastically cut down on mispacked goods and disappointed customers.
Picking is locating and retrieving products from your inventory using guided, barcode-driven workflows that confirm the right items are selected.
Packing is securely enclosing those items in the correct box or envelope, adding shipping labels, invoices, and protective materials, and verifying order details one final time.
This straightforward, two-step system is the backbone of reliable order fulfillment. Nail it, and your small business delivers the accuracy and speed that turn first-time buyers into loyal advocates.
What Does Picking and Packing Involve?
The pick and pack process might sound straightforward, but a lot happens between “you’ve received a new order” and “the order is shipped.” Here’s a typical flow:
1. Order receipt
A customer clicks “Buy,” and the order enters your system. If you're not using an e-commerce store, you may have manually created the order via a spreadsheet or system. If you're using automated inventory management software, it’ll generate a digital sales order, streamlining the process.
2. Picking list generation
Next, it’s time to create the pick list. Manually compiling a pick list for multiple orders can be time-consuming. With pick and pack software, you can generate a pick list for several orders in just a few taps, saving you time and reducing errors.
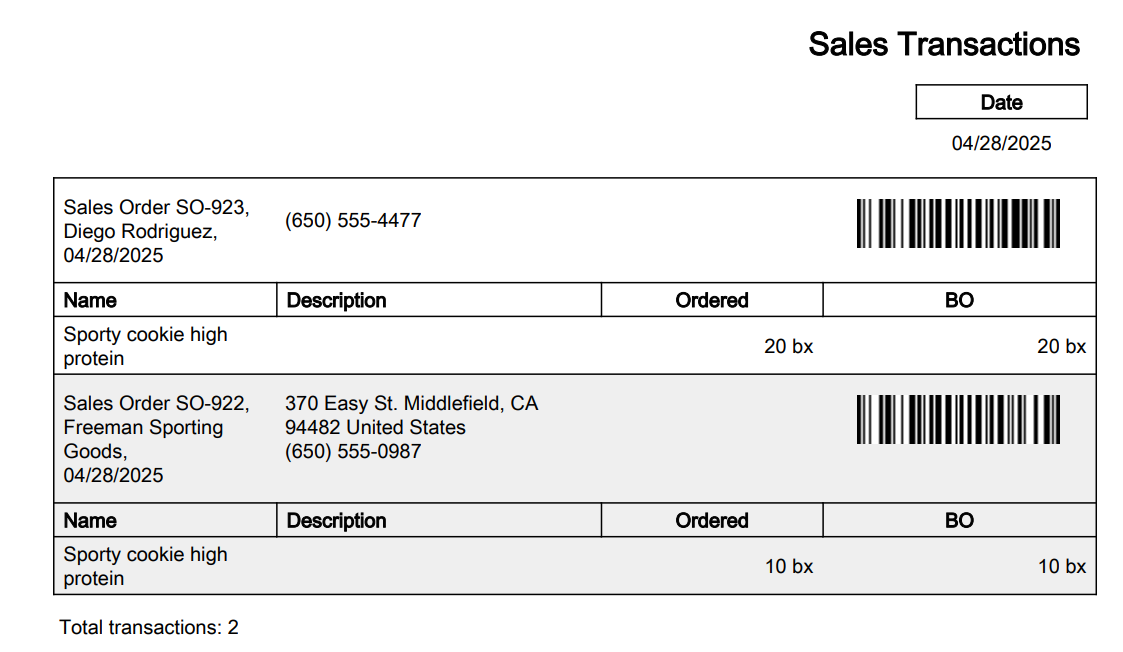
3. Item retrieval
Without bin location tracking, pickers often wander the warehouse looking for items, wasting valuable time. With automated inventory management, guided paths reduce the effort and time spent searching. Scanning barcodes confirms the right items are being picked.
This step also includes an inspection for any damage or mismatches, preventing returns and refunds down the line. Inaccurate stock levels or missing inventory can cause delays here.
4. Packing station setup
The packing process begins by selecting the appropriate box, adding padding, and ensuring the items are secure. If you're using automated fulfillment software, this step includes an extra layer of verification where items are scanned again during packing for accuracy.

5. Labeling and documentation
Next, you need to generate and print shipping labels, packing slips, and any customs forms (if necessary).
6. Carrier handoff
Finally, orders are grouped by carrier (USPS, UPS, local courier) and dispatched.
Each phase can introduce delays or errors. Identifying bottlenecks here is your first step toward faster, leaner fulfillment.
How to Optimize Pick and Pack?
1. Optimize warehouse layout
A well-organized warehouse is crucial for an efficient pick and pack process. Store fast-moving items closer to the packing stations to reduce travel time, and group similar products together. Regularly review and update the layout to ensure it adapts to changes in order volume and product lines.
2. Use barcode scanning for accuracy
Manual item selection can lead to errors. Implement barcode scanning to confirm product selection at each stage of the process, from picking to packing. This minimizes mistakes and ensures orders are accurate, improving customer satisfaction and reducing returns.
3. Batch and wave picking
Rather than processing one order at a time, consider batch picking where you pick items for multiple orders in one trip. Combine this with wave picking to organize orders based on priority or shipping method. This approach reduces downtime and speeds up the picking process.
4. Implement quality checks
Before packing, conduct a quick quality check to ensure the right items are selected and in good condition. This step helps catch mistakes early and prevents the costly repercussions of shipping incorrect or damaged products. Consider adding a second check at the packing station for extra accuracy.
5. Invest in packing optimization
Choose the right-sized packaging for each order to avoid excess shipping costs or product damage. Use automated packing tools if possible, which can recommend optimal packaging and streamline the process. Efficient packing not only saves on materials but also speeds up the fulfillment process.
6. Automate repetitive tasks
Leverage software for automated tasks like picking list generation and inventory updates. Automating these repetitive tasks frees up time for employees to focus on more critical parts of the process, such as order accuracy and quality control, ultimately boosting productivity.
7. Keep tabs on your order picking accuracy
Maintaining high order picking accuracy is crucial for retaining customers. Even minor errors, such as sending the wrong item, can lead to dissatisfaction and increased return rates. Implementing barcode scanning and real-time inventory tracking can significantly reduce picking errors.
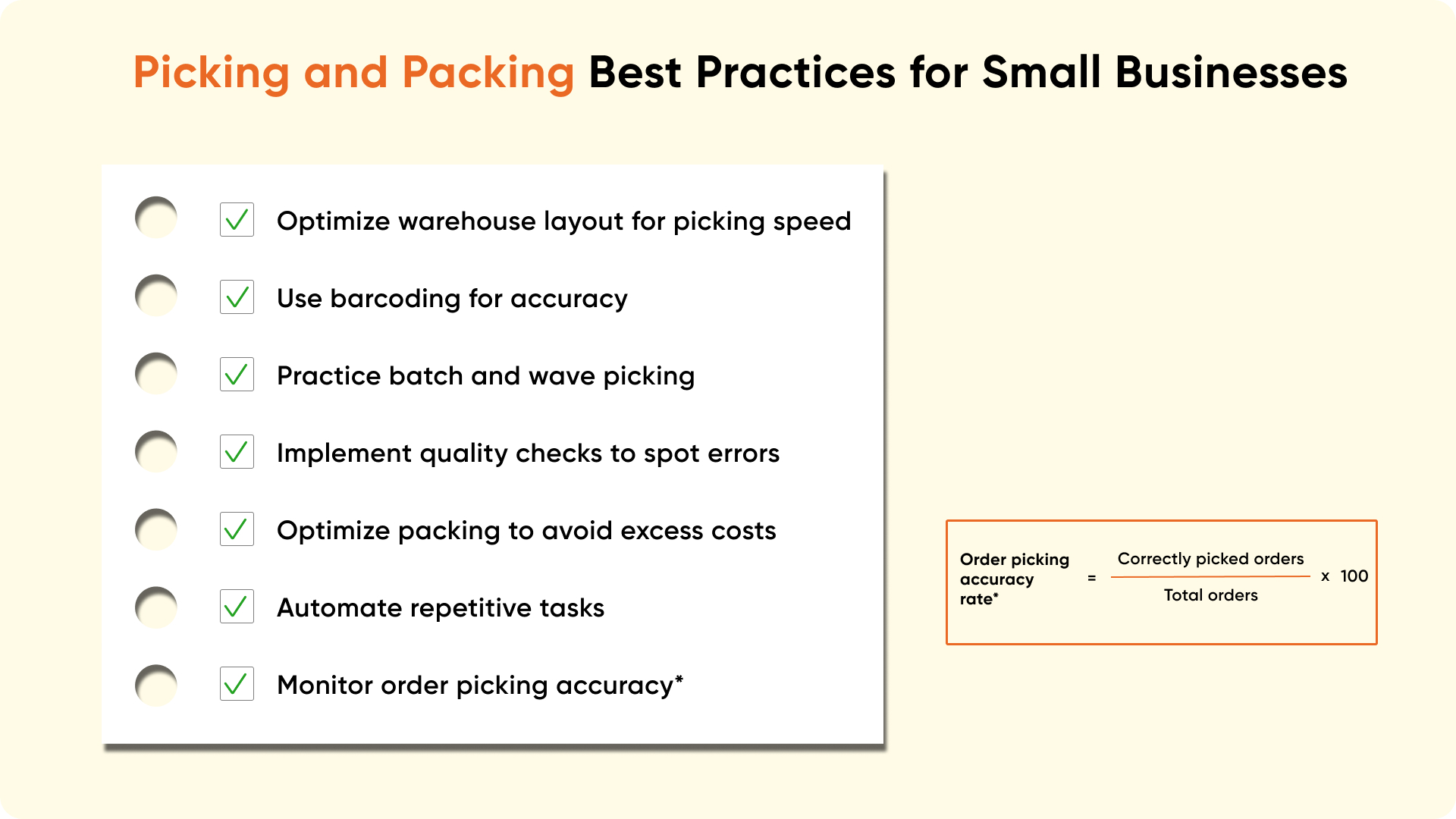
What’s your order picking accuracy rate now?
Order accuracy in top-performing businesses usually falls between 96% and 98%. This metric is calculated by dividing the number of correctly fulfilled orders by the total number of orders, then multiplying the result by 100.
The formula for calculating order accuracy is:
(Correctly Fulfilled Orders / Total Orders) x 100.
With a fully set-up and polished pick-pack process, you can achieve 98-99%. Here’s how.
How to Reduce Picking and Packing Errors with Pick and Pack Software
Manual processes are a mistake magnet. Software is the second set of eyes you wish you had when getting orders ready for shipment. When shopping for pick and pack software, look for these features:
Real‑time inventory synchronization
Inventory levels update instantly and across all platforms, warehouse facilities, and sales channels, with no overselling, no stockouts.
Bin location tracking
It’s a good idea to start tracking bin locations, so your pickers stop wasting time rummaging the warehouse for ordered SKUs.
Barcode scanning
Scanning items twice confirms correct products at pick, pack, and dispatch, virtually eliminating wrong‑item orders.
Partial picking/packing
The ability to pick and pack an order partially leaves no room for errors. The picker sees the order status and proceeds to look for missing items, generate a purchase order to get them quickly, or ship the order with a packing slip showing some of the items have been backordered.
Units of measure
You could be purchasing in one unit of measure, storing in another, and selling in a third one. You can pre-set your default units of measure and change them as you go.
Mobile access
Picking and packing are best done from mobile phones or tablets. On high-volume days, the packing station can be pretty crowded, so having a mobile device with a barcode scanning ability warrants less maneuvering from your warehouse workers.
By layering technology into your workflow, you swap guesswork for precision. And when your customers receive the right order on time, they return with rave reviews (and more orders).
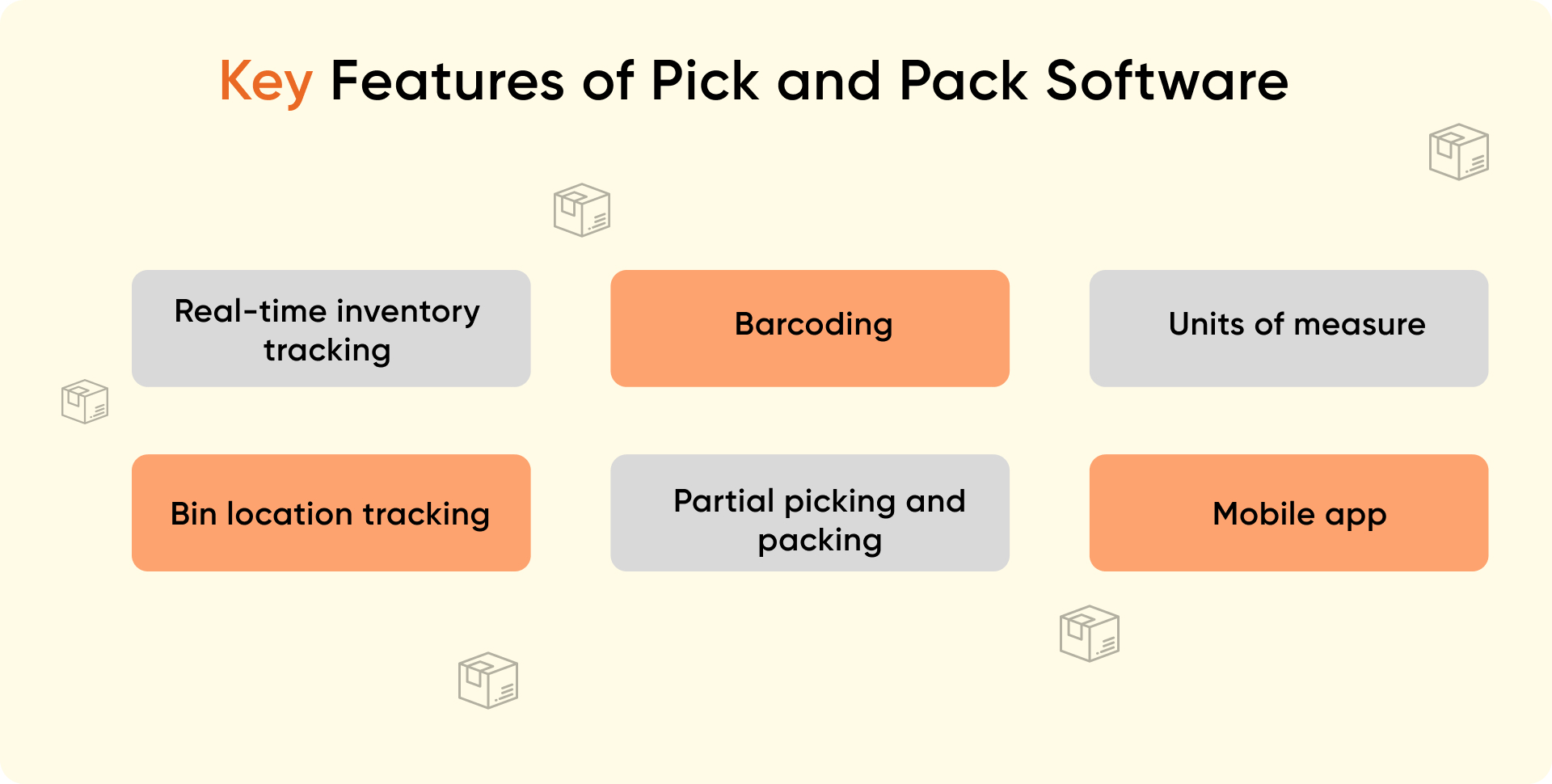
Why It Pays Off to Introduce Automated Order Fulfillment? (a HandiFox User’s Results)
The automated pick and pack process makes life way easier in the warehouse — here’s how it helps you move faster, smarter, and with way fewer headaches:
Automated order picking with pick lists
Automated pick lists guide your team step-by-step, slashing picking errors and speeding up the entire order fulfillment process.
Double verification for order accuracy
With double verification baked in, the software acts like a built-in quality control manager, catching mistakes before they ever reach your customer.
Packing slips for customer transparency
Packing slips show customers exactly what’s inside the box, building trust, reducing disputes, and setting the stage for repeat business.
Increased warehouse throughput
Faster, more accurate picking and packing means more orders flying out the door each day without adding extra staff or chaos.
Reduced manual intervention in fulfillment
Automating key steps minimizes the risk of human error and frees your team to focus on higher-value tasks instead of babysitting inventory.
Minimized time spent on repetitive tasks
By handling repetitive actions like order sorting, label printing, and inventory updates automatically, the software gives your team hours of their day back.
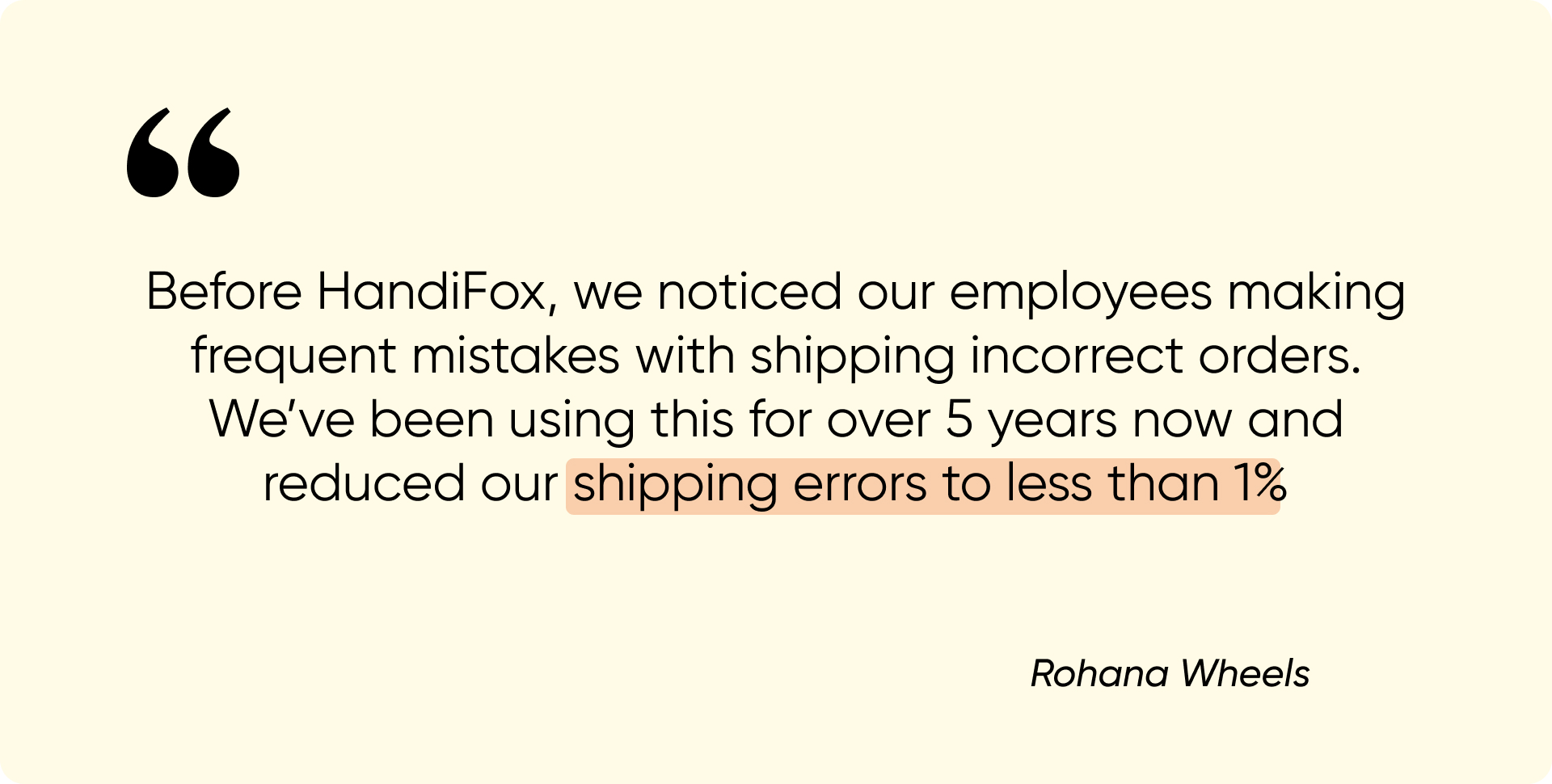
By layering technology into your workflow, you swap guesswork for precision. And when your customers receive the right order on time, they return with rave reviews (and more orders).