Key takeaways:
- Reorder Point (ROP) and Par Level are the most suitable replenishment methods for small businesses, offering reliability, simplicity, and automation potential.
- Just-in-Time (JIT), Top-Off, and Periodic Review are less effective for small businesses due to reliance on perfect timing, overstocking, or unpredictable demand.
- Optimize stock replenishment on a budget: improve replenishment without spending by setting reorder points, factoring in vendor lead times, tracking sales velocity, and using simple tools like Excel to forecast needs.
- Small businesses can enhance inventory processes with affordable tools like HandiFox Online at as little as $39/month, automating purchasing and restocking.
- Features like mobile access, barcode scanning, and integration with existing tools (e.g., QuickBooks) increase speed, reduce errors, and improve overall stock control.

For small businesses, inventory is the heartbeat of your operation. When inventory runs low, customers leave empty-handed. When it piles up, your cash flow suffers.
Inventory replenishment is often managed manually, especially by small businesses operating on a tight budget. But here’s the truth: poor replenishment habits can cost you thousands annually in missed sales, overstock, and labor inefficiencies.
The good news is you don’t need enterprise software or a six-figure budget to fix it. By combining smart strategies with a $39-per-month purchasing software subscription, small businesses can streamline restocking, avoid inventory chaos, and operate with confidence.
Why Streamlined Warehouse Replenishment Matters
A tight handle on how you replenish inventory ensures:
- You have enough stock to meet customer demand.
- You avoid over-investing in slow-moving items.
- Your team spends less time scrambling to fill shelves.
- You improve vendor relationships with consistent purchasing.
Stock replenishment is about creating a sustainable rhythm that helps you make smarter purchasing decisions, improve cash flow, and not overextend your staff.
What Inventory Replenishment Methods Work Better for Small Businesses?
There are several ways to approach inventory replenishment, and the best choice depends on your product mix, cash flow, supplier relationships, and operational workflow. Below are the most common replenishment methods:
- Reorder Point (ROP): Automatically reorder an item when its stock level falls to a pre-set threshold.
- Par Level: Maintain a fixed “ideal” stock level and reorder only what’s needed to reach that level.
- Just-in-Time (JIT): Order inventory only when it’s needed, reducing storage costs but increasing reliance on fast supplier delivery.
- Top-Off: Restock as much inventory as possible within storage constraints, often used to maximize space or truck capacity.
- Periodic Review: Replenish stock at regular time intervals (e.g., weekly, monthly), regardless of actual inventory levels.
ROP and Par Level are generally better aligned with the realities of running a small business, where resources are tight, flexibility is key, and manual processes can create costly errors. Here’s why:
Reorder Point (ROP)
Reorder point (ROP) is the most popular method among small businesses, and for good reason. It’s simple, reliable, and easy to automate. You set a threshold (the reorder point), and once inventory drops to that level, it triggers a reorder. ROP works best when paired with lead time data and average daily usage.
Par Level
Par level replenishment is ideal for businesses that perform routine visits to customers or branches, like beverage or food distributors. It maintains a “desired” stock level and replenishes the difference. This method is less dynamic than ROP but fits well into a repeatable workflow, especially when managing consigned stock or remote inventory sites.
Why do JIT, Top-Off, and Periodic Review Not Work for SMBs?
Just-in-time (JIT) replenishment, where stock is ordered only when needed, is often too risky for small businesses. While it minimizes storage costs, it depends heavily on perfect timing and highly reliable suppliers. A single delay can halt operations. For most small businesses, JIT is better suited as a complementary tactic for non-critical or slow-moving items.
Top-off replenishment seems convenient, especially when trying to fill delivery trucks efficiently or keep shelves full. But it often leads to overstocking, especially with slower-moving items. For small businesses watching every dollar, tying up cash in low-priority products just to “fill the space” can create more financial stress than it's worth.
Although periodic review is easy to schedule, this method assumes that your demand is predictable and steady. That’s rarely the case for small businesses, where sales can fluctuate due to seasonality, promotions, or supplier delays. You might reorder too early or too late.
You don’t have to pick just one method. Many small businesses use a combination, for example, ROP for warehouse stock and Par Level for field replenishment. Choose what aligns with how you work today.
.jpg)
How to Optimize Stock Replenishment Procedure Without Spending a Dime
Not every small business is ready to jump into full automation. But there are simple, budget-conscious steps you can take to improve your replenishment strategy today:
Step 1: Set Reorder Points and Desired Stock Levels
Use past sales data to determine minimum stock levels. When inventory dips below that point, it's time to reorder.
Step 2: Factor in Vendor Lead Times
Build lead time buffers into your reorder process. For example, if a vendor takes 10 days to deliver, don’t wait until you’re out of stock to place an order.
Step 3: Track Sales Velocity (How Fast Items Sell)
Use basic reports to calculate average sales per day/week and forecast demand over the next reorder cycle.
Step 4: Create a Replenishment Worksheet
Even if you’re not ready for software, a well-structured Excel sheet can help forecast replenishment needs based on usage and vendor delivery cycles. Here’s a simplified version of what it might look like:

If you're managing all this manually and it's starting to break down, it might be time to let software do the heavy lifting.
Inventory Replenishment Software: Key Features
With the right purchasing software, you no longer rely on memory or clunky spreadsheets to know what needs to be ordered.
When evaluating purchasing software, look for these critical features tailored to small businesses:
1. Replenishment Forecasting
Forecast future stock needs using historical sales data.
2. Sales Statistics
Analyze product performance in real time. Understand what sells, how fast, and where, so you can restock smartly, not blindly.
3. Reorder Points and Desired Quantity Settings
Set minimum thresholds and preferred stock levels for each item. When an item drops below the reorder point, the system generates a replenishment order automatically..
4. Vendor Management
Maintain a central record of all vendor details, like pricing, lead times, contact info, and performance history, to make better purchasing decisions.
5. Multiple Vendors Per Item
Support for alternate suppliers gives you flexibility during backorders or pricing fluctuations. Compare pricing and availability across vendors in seconds.
6. Multiple Units of Measure per Item
Buy in cases, sell in eaches, and store in pallets? Your software should handle that. Accurate unit conversions prevent mismatched stock levels and invoice errors.
7. Mobile Access & Barcode Scanning
Replenish stock from the floor, truck, or warehouse with mobile devices. Use barcode scanning to verify current stock and create POs on the fly.
How to Implement Replenishment Software Without Breaking the Bank
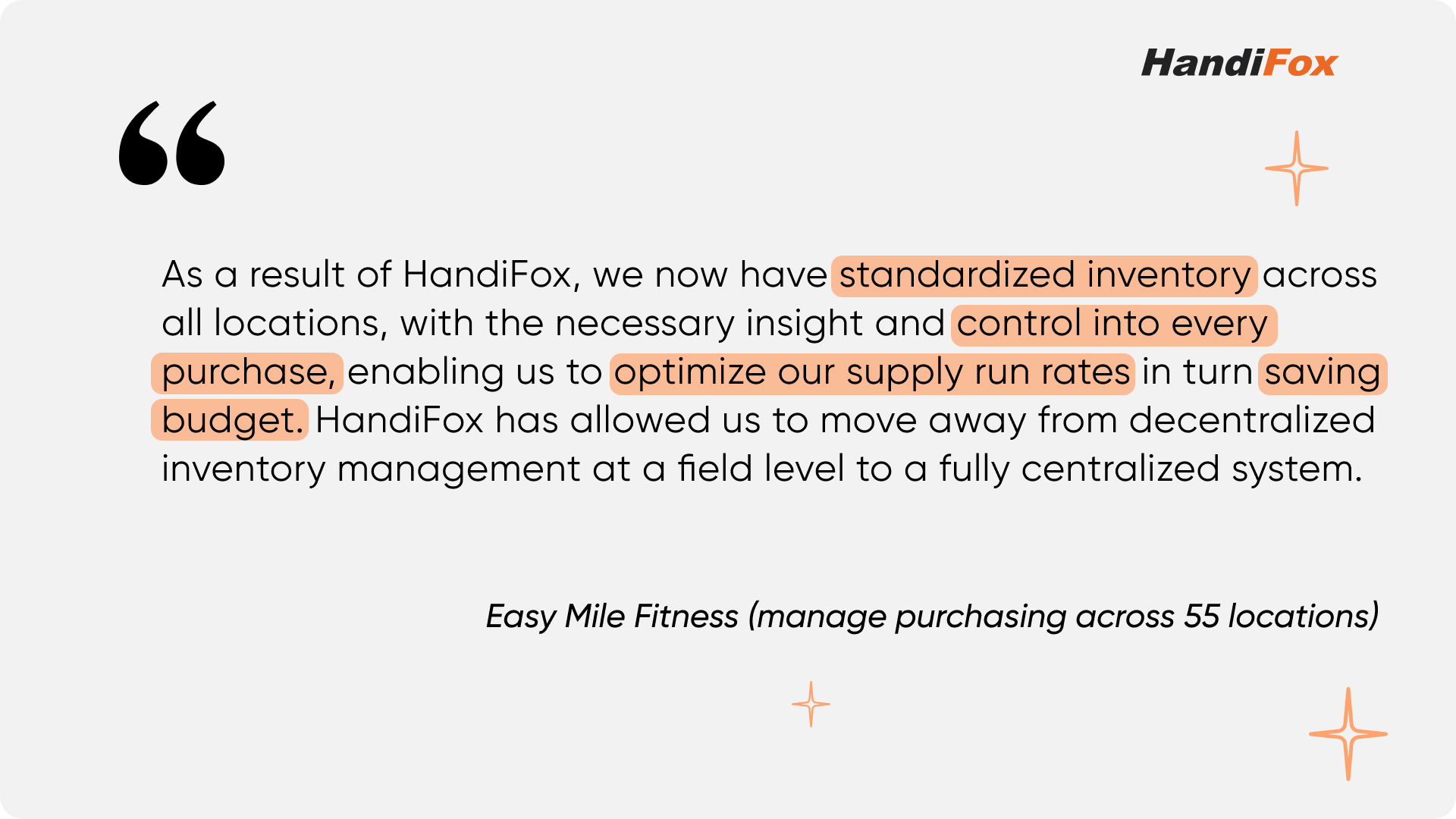
Small business owners often fear that an automatic inventory replenishment system means huge upfront costs, long setup times, and complex training. That’s not the case anymore.
Start Small
Choose a software plan that focuses on inventory and purchasing only, no need for bulky ERP features. For example, HandiFox Online’s Start tier at $30/month offers essential inventory and purchasing tools without overloading you.
Use Existing Tools
Look for software that integrates with systems you already use, like QuickBooks. That way, you avoid double-entry and ensure smooth workflows.
Go Mobile
Choose a solution with mobile access. Being able to replenish inventory from anywhere, including the warehouse floor or delivery vehicle, increases speed and accuracy.
Prioritize Must-Have Features
You don’t need every bell and whistle. Focus on reorder automation, vendor management, and mobile scanning to get the highest ROI first.
Get a Free Test-Drive of Automated Purchasing & Replenishment with HandiFox
Explore how HandiFox Online helps small businesses optimize purchasing and replenishment with features like
- Reorder points and Desired Quantity on Hand
- Automatic replenishment based on sales rate or reorder points
- Future restocking needs planning
- Mobile access
- Barcoding
- Alternate Vendors
- Multiple units of measure per item
- Bin location info
If automated purchasing and replenishment are what you’re missing, you’ll be good with the Start plan at $39/month. If you also need to automate your order fulfillment and sales, feel free to try the full-featured Pro version.