Key Takeaways
- Real-time tracking improves control. Accurate inventory data across all locations minimizes human error and supports faster decision-making.
- Automation delivers long-term savings. Inventory management software for multiple locations provides ongoing accuracy, eliminates redundancy, and scales effortlessly with your operations.
- Manual tracking becomes costly at scale. While spreadsheets and outsourcing may work initially, they lead to inefficiencies as location count grows.
- Upfront investment in tools pays off. Multi location inventory management software, apps, and scanners may require initial costs, but reduce long-term operational spend.
- Centralized systems reduce fulfillment errors. Synchronizing inventory management across multiple locations prevents miscommunication and improves customer satisfaction.
.jpg)
As businesses grow and expand into new warehouses, stores, or service areas, keeping track of inventory becomes more complex. Multi-location inventory management brings unique challenges that, if not handled properly, can lead to growing pains.
In this guide, we'll explore what multi-location inventory management is, the problems it solves, and how to approach it using the right tools and strategies.
What Is Multi-Location Inventory Management and Who Needs It?
Multi-location (or multi-warehouse) inventory management refers to the process of tracking and controlling inventory across multiple physical or virtual storage locations. These locations could include warehouses, retail stores, vans or service trucks, distribution centers, or even separate areas within a larger facility.
Businesses that operate in multiple regions or sell through multiple channels—especially wholesalers, retailers, manufacturers, and service providers—often require multi-location inventory tracking. Without a centralized system in place, it becomes easy to lose track of where products are, how much stock is available, and whether each location is adequately equipped to fulfill orders.
Having clear and reliable data on how your multiple warehouses are stocked cuts logistical costs, as you know where it makes more sense to pull inventory from instead of shipping from a distant warehouse.
Challenges of Managing Inventory Across Multiple Locations
When businesses scale without an effective system, they often encounter the following challenges:
Inconsistent Stock Levels
Determining purchasing budgets and replenishment needs across different locations is difficult without reliable data. One warehouse might be overstocked while another faces stockouts, causing lost sales and customer dissatisfaction. Overstocking ties up valuable capital and increases storage costs, whereas stockouts can drive customers to competitors. Frequent inventory transfers to balance stock levels add extra work and cost.
Lack of Real-Time Visibility
Without a centralized inventory system, businesses struggle to know exactly what's available at each location. Different tracking methods (manual counts, spreadsheets, or software) across locations produce vast, often confusing data. The lack of real-time updates leads to unexpected stockouts and delays. Additionally, poor visibility hampers quick responses to demand changes, as businesses can't easily identify surplus inventory at other locations.
Inefficient Fulfillment
Transferring products between warehouses without clear procedures creates confusion and delays. Orders may be mistakenly routed to warehouses lacking sufficient stock, resulting in rushed transfers and late or partial deliveries. These unplanned movements not only frustrate customers but also add unnecessary shipping costs, as goods often must travel longer or less efficient routes.
Manual Errors
Many small businesses still use manual processes or spreadsheets for inventory management, increasing the chance of mistakes. Typing errors, missed entries, and duplicated data quickly compromise inventory accuracy. Errors are magnified in multi-location setups—incorrect counts in one warehouse can skew company-wide data, causing inaccurate ordering and costly mistakes like stockouts or excess inventory.
Data Siloing
Inventory data stored separately at each location prevents a unified view of stock levels. Using different software, databases, or paper records at each warehouse creates data silos that don't automatically sync. Decision-making becomes difficult, as managers might reorder products that are abundant elsewhere simply due to a lack of visibility. Fragmented data leads to inefficiencies, duplicated efforts, and wasteful inventory practices.
Inconsistent Warehouse Processes and Training
Businesses often see different practices across locations when managing inventory. Without standard operating procedures (SOPs), each warehouse may handle receiving, transfers, and returns differently. This inconsistency results in errors and discrepancies in inventory records. Inadequately trained staff might mismanage simple tasks, such as recording inventory movements, leading to inaccurate data and operational confusion.
These issues not only impact operational efficiency but also customer satisfaction. Imagine promising a customer an item that shows "in stock" in your system, only to find it’s in a different location entirely.
How Do I Track Inventory in Multiple Locations Effectively?
.jpg)
If you're wondering how to track and manage inventory in multiple locations, the answer lies in adopting structured processes and supportive technology. Here are practical tips:
Assign Unique Identifiers
Every storage location should have its own unique identifier, such as a code or a descriptive name. Clear identifiers allow accurate tracking of inventory movements, help prevent mix-ups, and simplify audits.
Centralize Your Inventory Data
All inventory transactions should be recorded in a centralized, cloud-based system accessible from anywhere. Centralization ensures consistency, real-time updates, and easy cross-referencing of stock across locations, eliminating confusion from scattered data sources.
This said, centralized inventory control isn’t a one-size-fits-all approach. Small businesses operating overseas have to factor in local market conditions and unique regional demands. Also, if the centralized system faces operational disruptions (power outages, technology failures, or natural disasters), the entire inventory operation becomes vulnerable.
Establish Clear Transfer Protocols
Create clear and documented procedures for transferring inventory between locations. Include steps for initiating transfers, approvals required, documentation standards, and expected turnaround times. Clear protocols minimize errors, improve accountability, and keep operations smooth.
Set Location-Specific Stock Thresholds
Configure reorder points and safety stock levels individually for each location based on local demand patterns. This prevents inventory shortages or excessive overstocking, optimizing capital usage and ensuring consistent product availability across warehouses.
Regular Cycle Counts and Audits
Schedule regular cycle counts and inventory audits for each location. Frequent audits identify discrepancies early, allowing quick resolution before issues escalate. Regular counts maintain accuracy, reliability, and accountability in inventory records.
Ensure Real-Time Visibility with Inventory Tracking Software
Implement inventory tracking software that offers real-time data synchronization across locations. Real-time visibility helps identify stock imbalances instantly, streamlines decision-making, and allows quick adjustments in response to changing conditions.
Despite all the effort and manual work, tracking stock by hand quickly becomes unsustainable as operations grow. That’s where multi location inventory management software comes in.
Why You Need Inventory Management Software for Multiple Warehouses
Choosing the right inventory management software for multiple locations is key to solving these challenges. Here’s why multi-site inventory tracking is a massive game-changer:
Real-Time Stock Visibility
Inventory management software lets you monitor inventory levels across all locations from a centralized dashboard. You can instantly see stock status, detect shortages, and quickly address imbalances. Real-time visibility enhances decision-making and helps avoid stockouts, overstocks, and negative inventory.
Accurate Order Fulfillment
Advanced inventory software automatically matches customer orders with the nearest warehouse holding the required items, speeding up deliveries and reducing shipping costs. It also prevents errors that occur when manually checking inventory levels, ensuring higher customer satisfaction.
Streamlined Transfers
Simplifying inventory transfers between warehouses reduces operational friction. Clear workflows within inventory software help staff quickly move products, document transfers clearly, and reduce delays or miscommunication.
Better Reporting
Inventory management software generates comprehensive reports by location, item, or transaction type. These insights help business owners make data-driven decisions on purchasing, replenishment, and distribution strategies.
Compartmentalized Management
Inventory software supports compartmentalized warehouse management, enabling you to assign specific permissions to staff members at different locations. This approach enhances productivity by allowing teams to manage their warehouses independently while you focus on strategic oversight.
Standardized Procedures and Easier Training
Standardized inventory management software encourages uniform processes across all warehouses. This consistency simplifies employee training, reduces mistakes, and makes onboarding new staff faster and easier. It also simplifies financial reporting, especially when integrated with accounting platforms like QuickBooks Online.
Improved Purchasing and Replenishment
Effective software tracks sales history per location, making it easier to determine accurate purchasing budgets and reorder points. By understanding location-specific demand trends, businesses can optimize stock levels and avoid costly inventory mistakes.
Reduced Inventory Costs
Real-time visibility and streamlined inventory transfers enable businesses to operate with leaner inventories. Efficient inventory management reduces holding costs and prevents cash from being tied up unnecessarily in excess stock.
Easier Expansion
As businesses expand into new markets, multi-location inventory software ensures operational efficiency remains intact. Adding new locations within the software is simple, allowing companies to scale smoothly without disruptions.
Most importantly, multiple warehouse inventory management software reduces the need for manual updates and syncs data across departments, so everyone works with accurate, up-to-date information.
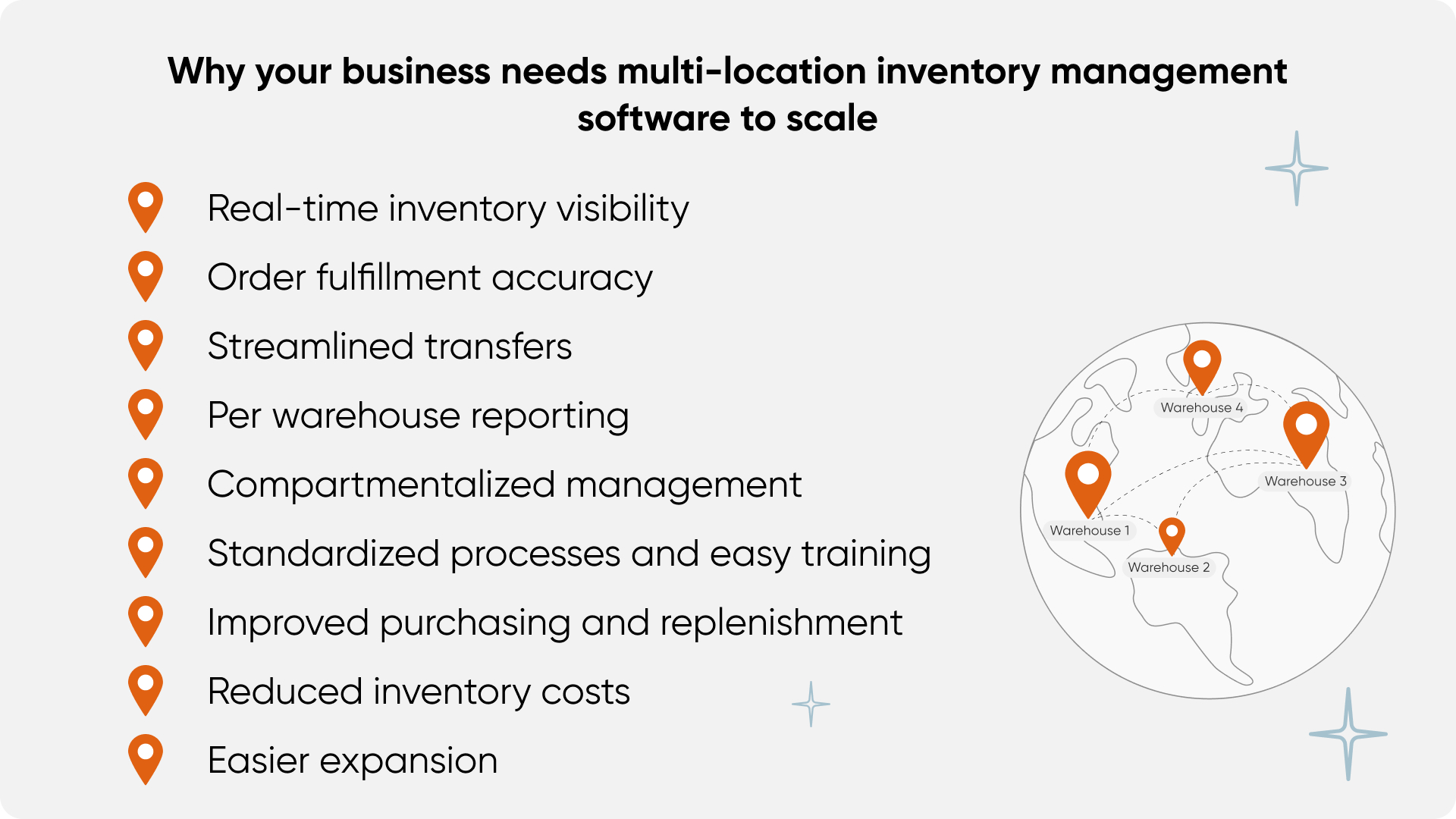
Top Features to Look For in Multi Location Inventory Management Software
Not all software is created equal. When shopping for multi-warehouse inventory management software, consider checking out these must-have features:
- Location-specific tracking. Ensure the system allows you to track quantities by location.
- Mobile access. Field teams and warehouse staff should be able to check and update inventory from mobile devices.
- Barcode scanning. It speeds up receiving, picking, and transferring items while minimizing errors.
- Inventory transfers. The ability to initiate and track cross-location transfers is essential.
- User permissions. Assign roles and restrict access based on location or responsibility.
- Per-warehouse reorder triggers.The ability to determine restocking thresholds for alerts and automated replenishment orders per warehouse or across all locations at once.
- Integration with accounting software. If you use accounting software like QuickBooks Online, integration with your multi-location inventory app ensures financial data and stock records stay aligned.
How HandiFox Helps Manage Inventory Across Geo-Distributed Locations (+ Success Story)
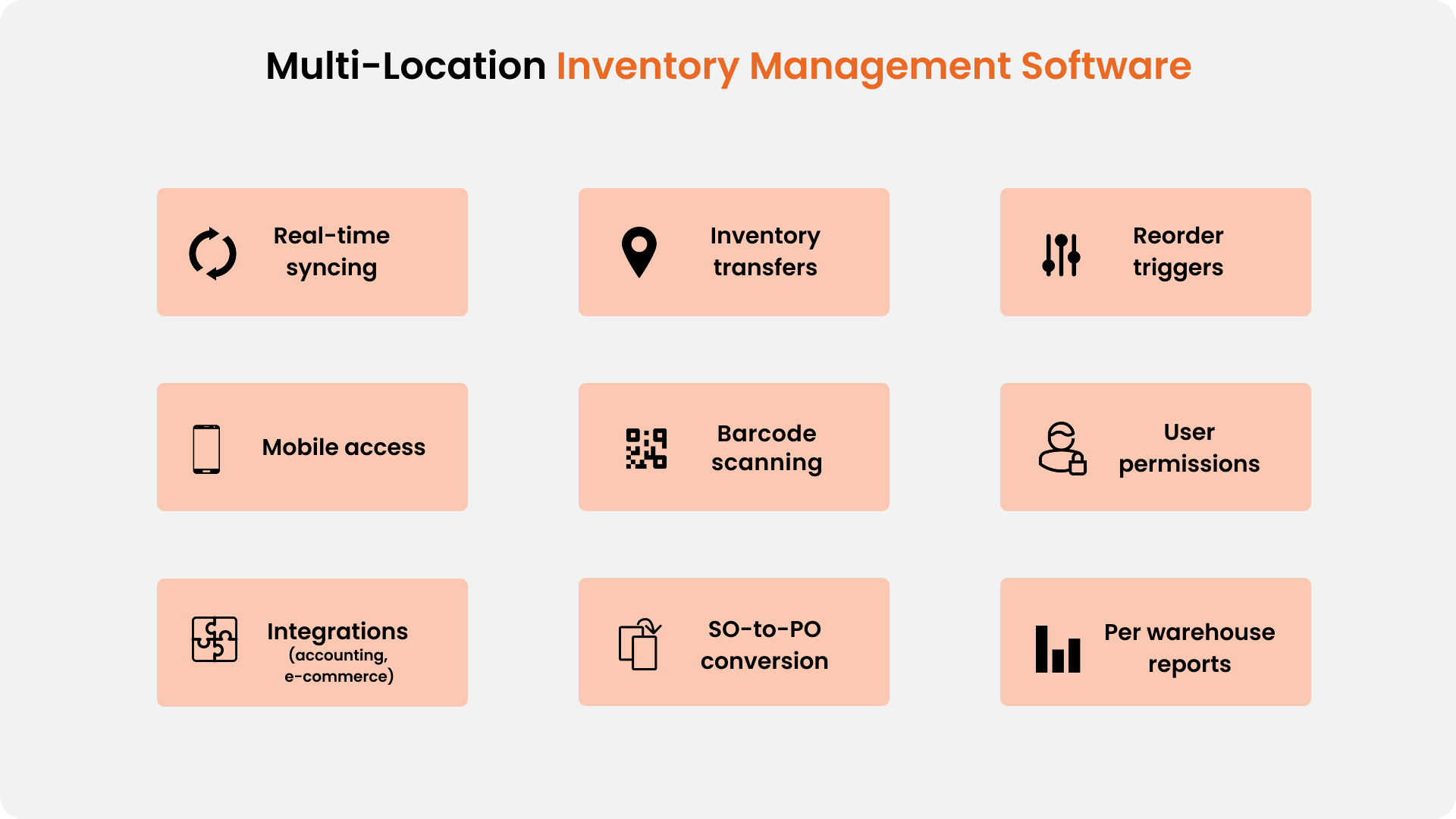
HandiFox Online supports growing businesses in tracking their inventory by location, moving stock between warehouses or vehicles, automating replenishment, and selling based on real-time product availability.
You can assign mobile devices to locations outside the country/city for distributed mobile inventory control. It’s easy to check how much inventory is on hand per warehouse or in total with HandiFox’s Quantity On Hand Viewer.
Moving inventory between your digital warehouses takes seconds and is logged like any other inventory movement within the system. You can restock per location based on pre-determined reorder points.
Every transaction is barcode-enabled for quick data entry and product search, streamlining adding and subtracting stock from the system. Check our guide for the best barcode scanner picks for 2025 here.
Here are a few more added-value features that make HandiFox a top choice:
- It’s a mobile-ready solution with native Android and iOS apps that let teams manage inventory from the field or the warehouse floor.
- If your’re dropshipping, there’s an instant one-click sales-order-to-purchase-order conversion that saves big on manual data entry.
- Thanks to the Sales by Location report, there’s a bird’s-eye view of how each location is performing.
When we say we’ve seen our customers grow, we mean it. When we met Easy Mile Fitness, they had 8 inventory locations. Now they are managing 55 inventory sites with HandiFox Online:
"HandiFox has enhanced our inventory management capability significantly. As a result of HandiFox we now have standardized inventory across all locations, with the necessary insight and control into every purchase, enabling us to optimize our supply run rates in turn saving budget. HandiFox has allowed us to move away from decentralized inventory management at a field level to a fully centralized system."
Philip Amato, COO Easy Mile Fitness