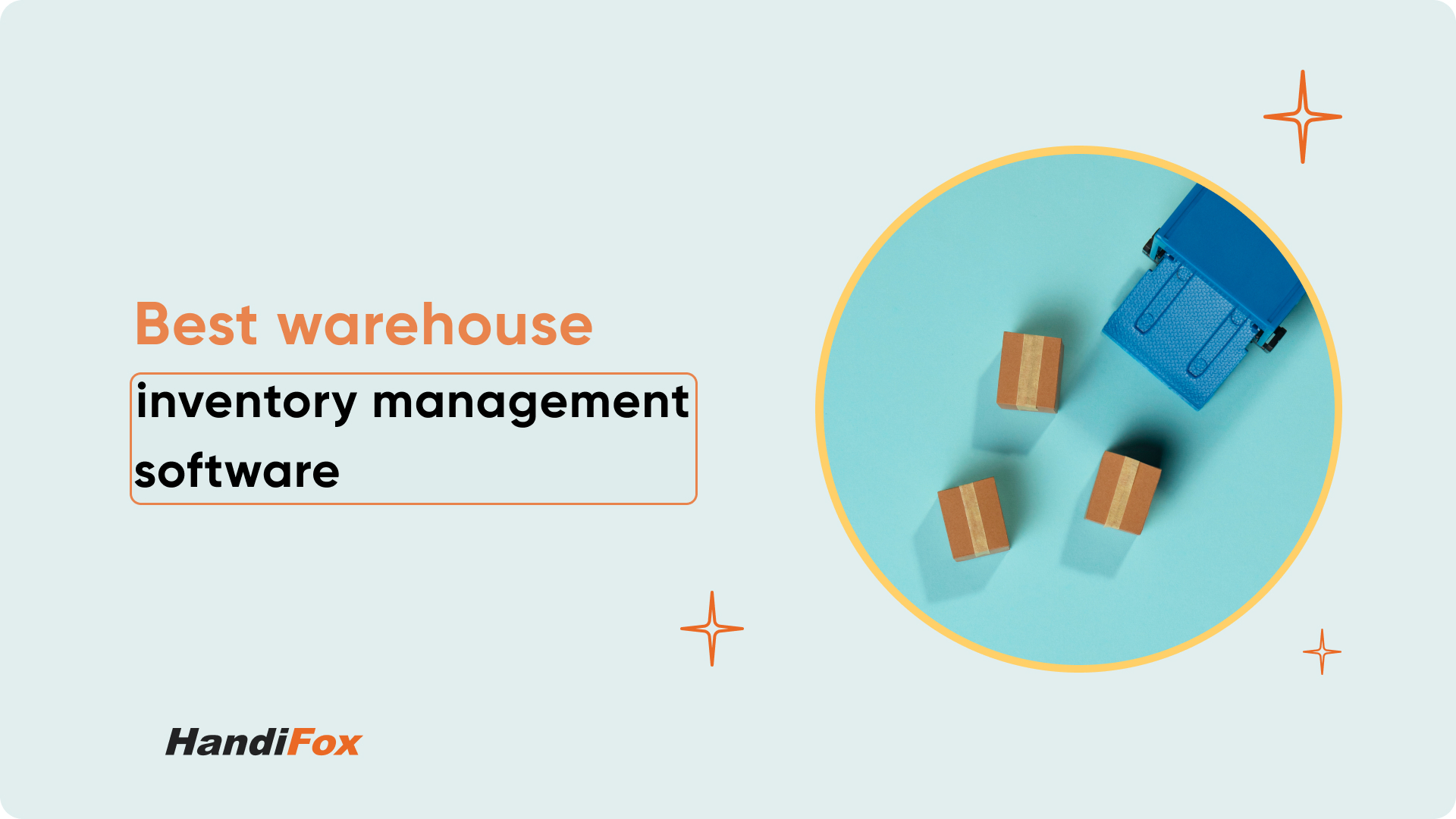
Warehouses are no longer just places to store products. In a modern business landscape shaped by e-commerce growth, supply chain volatility, and rising customer expectations, your warehouse is a mission-critical hub and the software that manages it determines whether your operations stay ahead or fall behind.
A warehouse software management system (WMS) empowers businesses to optimize inventory movement, track goods in real-time, reduce manual errors, and increase fulfillment efficiency. Whether you’re managing a single warehouse or coordinating distribution across multiple regions, the right system gives you the tools to streamline operations, improve data visibility, and scale with confidence.
In this article, we’ll explore the key functions of warehouse software, benefits by business type, and the core features to look for in 2025 and beyond.
What Is a Warehouse Software Management System?
A warehouse software management system (WMS) is a digital platform that helps businesses control and optimize the daily operations within a warehouse. From receiving and put-away to picking, packing, and shipping, WMS automates and coordinates workflows while maintaining an accurate inventory database.
Unlike simple stock tracking tools, a WMS offers detailed control over warehouse layout, inventory slotting, employee performance, cycle counts, and order routing, all while integrating with your accounting and sales platforms.
Why Warehouse Software Is Essential
Warehouses are the backbone of the supply chain, and delays or inaccuracies here ripple across every part of the business, from inventory planning to customer service.
Implementing a warehouse software system can help businesses:
- Reduce picking and packing errors
- Automate inbound and outbound logistics
- Track inventory across bins, shelves, and locations
- Improve order accuracy and reduce returns
- Enhance visibility with real-time dashboards
- Increase warehouse throughput without increasing labor costs
The result is faster delivery, fewer mistakes, and a more agile operation ready for scale.
Core Features to Look for in a WMS
1. Real-Time Inventory Control
A modern WMS gives you a live view of what’s in stock, what’s in transit, and what’s being picked or packed. This is especially useful for businesses that manage inventory across multiple warehouses or fulfillment centers.
Bonus tip: Choose a WMS that tracks not just quantity, but location - down to bin, zone, or shelf.
2. Mobile Scanning and Barcode Support
One of the most significant upgrades in warehouse management over the last decade is mobile barcode scanning. Instead of relying on paper pick lists or desktop input, warehouse workers can use handheld scanners or mobile apps to:
- Receive goods
- Scan barcodes
- Confirm picks and shipments
- Perform inventory counts on the go
3. Order Picking Optimization
An efficient WMS supports multiple picking strategies: wave, batch, zone, or FIFO, and allows for smart route suggestions to minimize travel time inside the warehouse. This reduces labor costs and increases throughput.
4. Purchase and Receiving Automation
When paired with inventory management software, your WMS should allow for automated creation of receiving documents, checking items against purchase orders, and reconciling discrepancies.
5. Cycle Counting and Auditing
Instead of shutting down your warehouse for a full inventory count, cycle counting allows you to verify smaller portions of inventory on a rolling schedule, improving accuracy without disrupting daily operations.
6. Multi-Warehouse and Multi-Location Support
If your business manages inventory across multiple sites, a centralized WMS becomes critical. It should allow you to:
- View inventory across all facilities
- Transfer goods between warehouses
- Apply location-specific rules and workflows
7. Integration with Accounting and ERP Systems
A good WMS should not function in isolation. It must sync with your accounting system, such as QuickBooks, to:
- Update COGS and stock values
- Create and reconcile invoices
- Match receipts with purchase orders
- Maintain financial accuracy in real-time
Benefits by Business Type
Retail and E-Commerce
Fast-moving inventory, high SKU volumes, and fluctuating demand mean that e-commerce businesses benefit tremendously from warehouse automation. A WMS helps ensure:
- Accurate order picking
- Quick returns processing
- Seamless integration with online stores
Field Sales and Service
For companies delivering from vans or local depots, a mobile-compatible WMS ensures inventory is tracked properly by reducing lost inventory and improving field accountability.
Manufacturing and Assembly
Manufacturers require deeper visibility into component inventory, assemblies, work orders, and bill of materials (BOM). A warehouse system should track not only finished goods, but also raw materials and subassemblies.
Wholesale and Distribution
For distributors, speed and accuracy are everything. A WMS reduces touchpoints and supports bulk receiving, batch picking, and route optimization, all of which boost efficiency.
Key Questions to Ask Before Implementation
- How many SKUs do we manage?
- How often do we receive and ship inventory?
- How many users need access (warehouse + back office)?
- Do we require integration with QuickBooks or another accounting system?
- Will we need mobile devices or barcode scanners?
- Do we manage serialized or lot-tracked inventory?
Understanding your current and future operational needs helps ensure that your warehouse software investment pays off.
Common Mistakes When Managing a Warehouse Without Software
- Mismatched inventory counts between physical and digital records
- Overstock or dead stock due to lack of real-time data
- Frequent delays in order fulfillment and shipping
- Relying on spreadsheets or manual logs for movement tracking
- Lack of accountability for warehouse team actions
All of these challenges create friction in daily operations and make it harder to scale. A WMS brings clarity, automation, and structure, transforming chaos into process.
Why HandiFox Is a Practical WMS Solution
While many enterprise platforms promise powerful warehouse features, they can be overly complex or costly for small to mid-sized businesses. HandiFox offers an alternative:
- Built specifically for businesses using QuickBooks
- Provides real-time mobile access and barcode scanning
- Manages warehouse-level tasks like receiving, picking, transfers, and cycle counts
- Affordable, scalable, and designed to simplify daily operations
For businesses not ready to implement a full ERP but needing more control than spreadsheets or manual systems, HandiFox offers a streamlined, effective path forward.
Summary
Warehouse software management systems have become a vital tool for businesses aiming to improve fulfillment speed, reduce error rates, and handle growing operational demands.
The right WMS will:
- Offer mobile and barcode support
- Track inventory accurately across multiple locations
- Improve order picking and packing
- Integrate with your accounting system
- Scale with your business as it grows
When combined with a user-friendly interface and thoughtful onboarding, warehouse software becomes one of the most valuable operational investments you can make.
Final Thoughts
Your warehouse is not just a storage facility, it's a dynamic part of your customer experience. With rising demand for fast, accurate, and traceable deliveries, businesses must equip their teams with the right tools.
A modern warehouse software management system transforms inventory chaos into coordinated control. Whether you’re a small wholesaler, a regional retailer, or a growing e-commerce operation, choosing a flexible, mobile-friendly, and integrated system can unlock new levels of efficiency.
To see how HandiFox supports real-time warehouse operations and integrates seamlessly with QuickBooks, request a demo or explore our blog for practical insights.